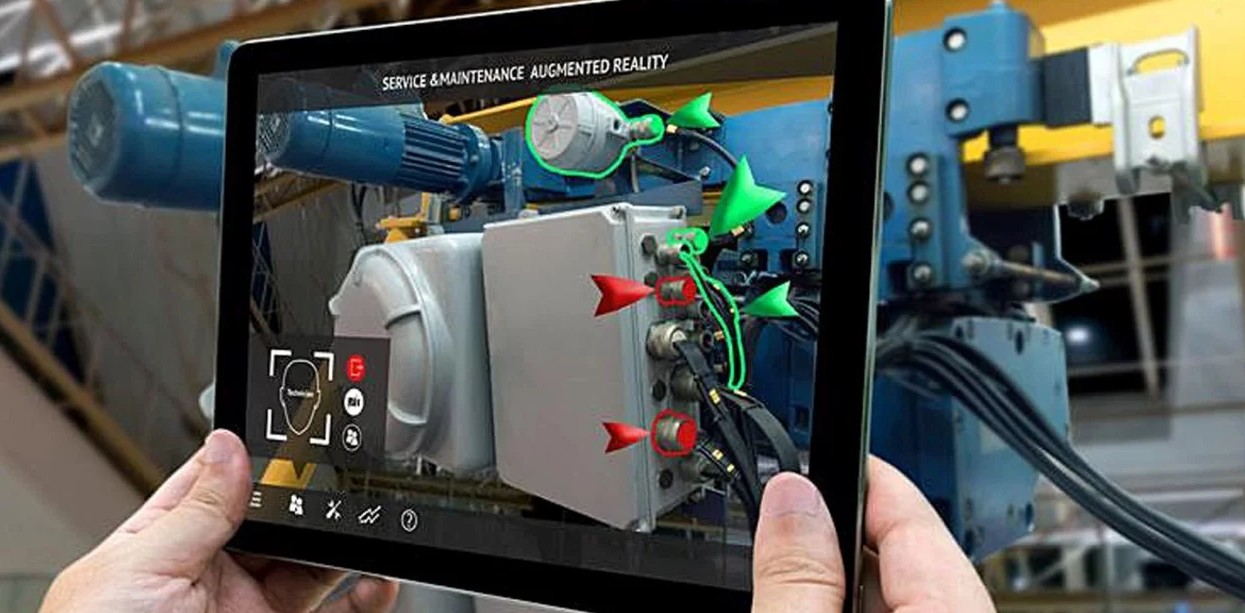
- Fecha 1 marzo 2020
- Autor Claudio Aveiro
- Tags argentina, educación, industria, revolucion
La nueva revolución tecnológica Industrias 4.0: la fábrica inteligente llegó a la Argentina
YPF, Acindar, Tenaris, Arcor y Aysa, entre otras, incorporan inteligencia artificial y Big Data en sus plantas.
Finalmente, y después de los avances registrados en la banca, el comercio y servicios, la incorporación de nuevos procesos automatizados basados en inteligencia artificial y Big Data está modificando el panorama en sectores industriales, como el petrolero, siderurgia, alimentación, electricidad, construcción, minería y hasta gestión de agua. En los últimos dos años, se sumaron a la movida varias empresas, entre ellas YPF, Vista, Techint, Acindar, Aysa, Tetra Pack, Arcor y Toyota, consideradas como las pioneras en el ámbito local de la llamada 4° Revolución Industrial.
Esa fuerte reconversión industrial fue uno de los ejes del último Innovation Summit, uno de los principales eventos anuales que organiza Schneider Electric, que se desarrolló entre el 2 y 3 de octubre pasado en Barcelona y al que acudieron más de 3.500 ejecutivos y expertos en energía y tecnología de todo el mundo. En el discurso de apertura, el CEO de Schneider, Jean Pascal Tricoire, dijo “nuestra generación se enfrenta a un cambio tectónico en la transición energética y la revolución industrial”.
Esa transición también se refleja en el modelo de negocios de Schneider, un gigante francés cuyo foco es proveer equipamiento para la transmisión y distribución de electricidad y que factura anualmente US$26.000 millones. Su otro gran negocio, el de mayor crecimiento y que ya le reporta el 23% de sus ingresos, son las tecnologías para la automatización industrial. En la Argentina, tiene clientes de la talla de YPF, Aysa, Tetra Pack, Tenaris y Ternium (ambas del grupo Techint) y el Hospital Italiano.
“Esas tecnologías nos permiten optimizar en tiempo real el funcionamiento de los pozos y se concentra en los recursos no convencionales de Vaca Muerta”, explicó una fuente de YPF. Existen diversas aplicaciones para el rubro petrolero. Una de ellas es un combo de sensores y equipamiento de Machine Learning, que regula y corrige el sistema de bombeo en un pozo para incrementar la producción y prevenir fallas.
El arsenal tecnológico es mucho más amplio. Uno de los más difundidos es el uso de la realidad aumentada para controlar grandes fábricas desde una tableta, abastecida con datos precisos y detallados de todas las áreas de una planta. “Uno de los objetivos es el mantenimiento predictivo, que nos permite prevenir desperfectos”, explicó al Económico el CIO de Acindar, Mauricio Gaggioli. Así, un operario coloca la tableta sobre un área y sobre la imagen aparecen alertas en los procesos productivos.
El mantenimiento predictivo es usual en fábricas de gran superficie. El objetivo es simplificar las tareas de supervisión a través de un tablero de control virtual, que releva todas las operaciones de la planta en pocos segundos. “En cada máquina hay un sensor que recolecta información (temperatura, vibración, consumo energético). Así, con el uso de inteligencia artificial, es posible predecir inconvenientes y corregirlos”, explica Diego Yanni, responsable del área digital de la consultora Accenture.
Estos casos incipientes reflejan los cambios acelerados en el sector fabril, que viene bastante rezagado con respecto a la banca digital y el comercio electrónico. La industria 4.0, en teoría, implica el uso de la inteligencia artificial, el proceso automático de enormes cantidades de datos y el armado de una red interconectada de sistemas y dispositivos electrónicos. “La transformación se produce -aclara Yanni- cuando se lo implementa a escala en toda la cadena productiva”.
La aclaración tiene que ver con que muchas empresas están en fase de experimentación. Por caso Arcor, que tiene un programa “Industria 4.0” para reformular sus plantas, o Toyota, que está ensayando un sistema de mantenimiento predictivo de última generación. Algo más adelantada está YPF, que además de contar con sistemas inteligentes de extracción y exploración petrolífera y gasífera, implementó un “control remoto de telesupervisión, que integra el ciclo integral desde el pozo hasta la sala central de operación”.
No se trata de una modernización de los circuitos de producción, sino un salto cualitativo para incrementar la productividad y reducir costos para competir en los mercados internacionales. “El 80% de los tubos de acero sin costura que produce Tenaris en su planta de Campana se destina a la exportación”, explican. Con una dotación de 5.000 empleados, la compañía instaló un “simulador de grúa” dotado de un casco de realidad virtual para capacitar al personal en el manejo de los controles.
Tenaris es pionera en el camino hacia la industria 4.0. Hace 2 años aceleraron los programas de transformación industrial, que incluye también un proceso inteligente de control parcial de calidad de la producción de tubos sin costura, que también funciona bajo el esquema de realidad aumentada. “El sistema elabora estadísticas de todo el proceso y determina el porcentaje de fallos y el consumo energético en cada sector, entre otros”, dicen.
Aysa atraviesa ese ciclo transformador. Inicialmente, la empresa estatal de aguas automatizó todo el proceso (manejo de plantas, redes de distribución, redes cloacales y tratamiento de afluentes) con puntos de monitoreo para medir la calidad y la eficiencia. Pero por otro lado, Aysa ensaya un sistema de “mantenimiento predictivo”, con miras a implementarlo el año próximo.
Acindar inició ese camino a fin de 2017, argumenta Caggioli, como parte de un plan para digitalizar la producción: “Primero, identificamos los procesos a mejorar. Y el logro principal, hoy, es que disponemos de toda la información de la compañía en forma transversal y en tiempo real. Con eso logramos acelerar el proceso de toma de decisiones en todas las áreas de la compañía”.
Detrás de todo, está el consumo energético. En Schneider sostienen que casi todos los avances tecnológicos dependen de la generación eléctrica. En el Innovation Summit, Tricoire estimó que desde 1900 “el consumo energético se multiplicó 40 veces”. Más en detalle, el jefe de innovación tecnológica de la multinacional francesa, Emmanuel Larraguirre, sostiene que estamos “en medio de una revolución energética, muy similar a la tecnológica”.
De nacionalidad argentino, el alto ejecutivo estimó que el consumo eléctrico se duplicará en los próximos 20 años y que con el modelo de generación actual “será imposible cubrir la demanda”. Por tal motivo, Larraguirre interpreta que la era de las usinas y las represas tiene los días contados y que las grandes compañías eléctricas afrontan el desafío de reconvertirse “porque las que no se adecúen corren el riesgo de desaparecer”.
El modelo eléctrico del futuro, según describió, estará basado en la autogeneración de los usuarios, principalmente energía solar, que volcarán los excedentes a la red. “Cada vez habrá más empresas, fábricas, data centers, hoteles y hospitales produciendo su propia energía. Esta descentralización de la energía es la revolución que veremos”, dijo.
Según Larraguirre, en este nuevo contexto, el rol de las grandes compañías de electricidad será intermediar y equilibrar la oferta y la demanda. Propiciada por los avances tecnológicos, la energía descentralizada representa una facturación de alrededor de US$1.000 millones y en los próximos 10 años alcanzarían los US$200.000 millones. “En California, por ejemplo, se debate si conviene invertir en nuevas redes eléctricas”, finalizó. FUENTE: Damián Kantor
Y vos, estás listo para afrontar los nuevos desafíos?
EN NUT EDUCACIÓN TENEMOS LOS RECURSOS EDUCATIVOS PARA IMPULSAR TU CARRERA LABORAL, CONSULTANOS.